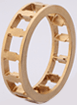
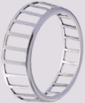
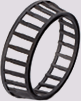
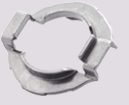
At Harsha, manufacturing excellence is driven on a philosophy of using new age technology to design and produce bearing cages and Stamped components with a focus on cost, quality and manufacturing flexibility.
Our tool room is equipped with machines like Hard Milling and Turning Machines, CNC Wire-cut and EDM Machines with rotary electrodes, Axis Machining centre and various high accuracy measuring instruments including CMMs to deliver precision quality products.
We use tool design software like Pro Engineer for 3D modelling and detailing, Numerically Controlled Tool Path, Auto Cad Stations, Sheet Metal Formability Simulation, Hyperworks which allows us to eliminate any deviation in the design process.
Harsha has been awarded - TPM Excellence Category A by Japan Institute of Plant Maintenance (JIPM).
Starting with 5S, Harsha uses a TEAM Concept (Together Everyone Achieves More), which focuses on total employee involvement and first person ownership for productivity and maintenance to achieve manufacturing excellence. Across the production base at Harsha, one observes TPM being effectively implemented through systematizing, sorting, sweeping, standardizing and self-discipline.
Our Research & Development initiatives have led through to innovations which have been instrumental in improving manufacturing processes, reduced human error, enhanced precision and saved energy across product verticals.
We also seek to capitalize on emerging trends such as very clean bearing to reduce noise by supplying clean cages, to develop right geometry of cage to reduce energy loss due to friction products.
Harsha adopts the best practices of Quality Systems to manufacture world-class precision components to meet the high expectations of global customers.
Our quality systems are certified as:
As Harsha continues its march towards a zero defect environment, it continues to ensure regular assessment, reviews, course correction and retraining to reaffirm its quality focus.
The manufacturing processes leverage a production infrastructure comprising of manual, semiautomatic and fully automatic machines. The multiple production bays comprise of: